For Particle Removal From Beer
Profile Star filter cartridges are pleated depth filters designed for high particle removal efficiency.The graded pore structure enables efficient particle removal while the star pleat configuration enables reverse flushing for extended filter life.
The Profile Star filter cartridge combines the advantages of a continuously graded pore structure and a unique pleated geometry to provide an increase in effective filtration area and service life. The pleat configuration enables effective low pressure backflushing to remove surface particles and enhance filter regeneration.
The pressure drop and flow capability is comparable to competitive pleated polypropylene filters whilst also providing excellent removal of soft contaminants (e.g. gels) because of the depth of the medium.
Features | Benefits |
Fixed fiber matrix |
|
Unique pleated medium with no sideseal |
|
Polypropylene filter construction with no adhesives or surfactants |
|
Food Contact Compliance
Please refer to the Pall website for a Declaration of Compliance to specific National Legislation and/or Regional Regulatory requirements for food contact use.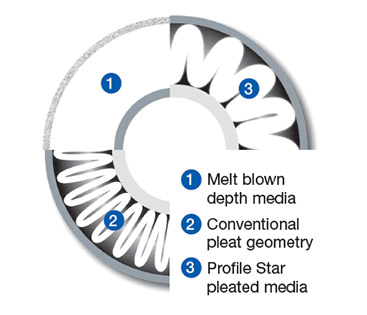
Materials of Construction
Filter Medium | Polypropylene |
Cage, Core, Fin End and End Cap | Polypropylene |
Adaptor | Polypropylene with stainless steel reinforcing ring |
O-Ring Seal | Silicone Elastomer Ethylene Propylene Rubber |
Technical Information
The technical information provided is based on controlled laboratory tests done on typical production filters at the conditions described, unless otherwise indicated. Actual operating conditions may affect the filter's performance.Operating Characteristics in Compatible Fluids1
Maximum Differential Pressure | Operating Temperature |
5.0 bard (72 psid) (forward) | <50 °C (122 °F) |
3.4 bard (50 psid) (forward) | <80 °C (176 °F) |
0.3 bard (5 psid) (forward) | <125 °C (257 °F) |
1 Fluids which do not swell, soften or adversely affect any of the filter components
Typical Flow Rates2
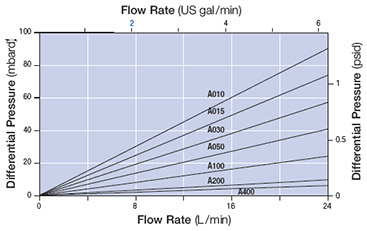
2 Typical initial clean delta p per 254 mm (10 inch) cartridge, water at 20 °C (68 °F). For liquids with viscosity greater than 1 cP, multiply the delta p by the viscosity.
Sterilization and Sanitization3
Method | Temperature | Cumulative Time |
Steam Sterilization | 125 °C (257 °F) | 10 hours |
Hot Water Sanitization | 80 °C (176 °F) | |
3 For applications requiring in situ sterilization or sanitization Pall recommends the use of Code 7 adaptors to ensure filter sealing after cooling. Cartridges should be cooled to system operating temperature prior to use.
Quality
- Cartridges produced in a controlled environment
- Manufactured according to ISO 9001:2008 certified Quality Management System
Beer (Craft/Micro Breweries), Beer (Craft/Micro Breweries), Beer (Craft/Micro Breweries), Beer (Corporate), Beer (Corporate), Beer (Corporate), Bottled Water, Bottled Water, Soft Drinks, Soft Drinks, Wine
Filter Cartridges
This information is a guide to the part numbering structure and possible options. For availability of specific options and housing details, please contact Pall.
Part Number: AB [Table 1] [Table 2] [Table 3] W [Table 4]
Example Part Number: AB3A0307WH4
See bold reference codes in tables.
4 Profile Star filter cartridge liquid retention ratings are based on a modified OSU-F2 single pass test.
Part Number: AB [Table 1] [Table 2] [Table 3] W [Table 4]
Example Part Number: AB3A0307WH4
See bold reference codes in tables.
Table 1: Nominal Length
Code | Length |
1 | 254 mm (10") |
2 | 508 mm (20") |
3 | 762 mm (30") |
4 | 1016 mm (40") |
Table 2: Removal Rating4
Grade | Rating (μm) at 99.98% Efficiency (ß-5000)5 | Rating (μm) at 99% Efficiency (ß-100) |
A010 | *1 | - |
A015 | *1.5 | - |
A030 | 3 | *1.6 |
A050 | 5 | 3 |
A100 | 10 | 7.5 |
A200 | 20 | 16 |
A400 | *40 | - |
4 Profile Star filter cartridge liquid retention ratings are based on a modified OSU-F2 single pass test.
5 The A010 grade has a 99.8% removal efficiency. Asterisks indicate extrapolated values.
Table 3: Adaptor
Code | Description |
3 | SOE - single open end with flat closed end and external 222 O-rings |
7 | SOE - single open end with fin end, 2 locking tabs and external 226 O-rings |
8 | SOE - single open end with fin end and external 222 O-rings |
28 | SOE - single open end with fin end, 3 locking tabs and external 222 O-rings |
Table 4: O-ring Seal Material
Code | Description |
H4 | Silicone Elastomer |
J | Ethylene Propylene Rubber |
Earn 10% off* your next order online by leaving a review of this product. Please login to your account to leave a review. We appreciate and value your feedback.
*Subject to Terms and Conditions.